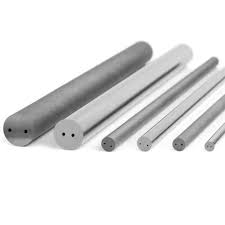
In the competitive world of CNC tool manufacturing, precision, consistency, and durability are non-negotiable. One of the foundational materials that determine these factors is the solid carbide rod—the core component for high-performance cutting tools like drills, end mills, reamers, and other custom tooling solutions.
As a CNC manufacturer, choosing the right solid carbide rod is critical to tool performance, customer satisfaction, and your brand’s reputation. In this guide, we’ll walk through the key considerations when selecting solid carbide rods.
What Are Solid Carbide Rods?
Solid carbide rods are cylindrical bars made from tungsten carbide, a composite material composed of tungsten carbide powder (WC) bonded with a metallic binder, typically cobalt (Co). These rods are prized for their extreme hardness, high wear resistance, and thermal stability—making them ideal for manufacturing precision cutting tools used in CNC machining.
Unlike coated or tipped tools, solid carbide tools are made entirely from this composite material, which enhances tool strength and enables consistent high-speed machining across tough materials such as stainless steel, titanium, and hardened alloys.
Why Material Quality Matters in CNC Tool Manufacturing
The performance of a CNC cutting tool depends heavily on the grain size, binder content, and sintering quality of the carbide rod from which it is made. Here’s why each of these matters:
A. Grain size: Fine grain carbides offer excellent toughness and are perfect for machining hard materials. Ultra-fine grain rods are widely used for micro-tools and high-precision cutting.
B. Binder content: A higher cobalt content increases toughness but may slightly reduce hardness. The right balance depends on the application (roughing vs. finishing).
C. Sintering process: Even and complete sintering ensures uniform microstructure, minimizing the risk of tool failure under high loads.
Key Factors to Consider When Choosing Solid Carbide Rods
When sourcing solid carbide rods for CNC tools, it’s important to evaluate the following technical and practical aspects:
1. Application Requirements
Are you manufacturing tools for aluminum, stainless steel, or hardened steel? Different materials require different carbide grades. For example:
For non-ferrous materials, use rods with high toughness and good chip flow.
For hard materials, opt for rods with ultra-fine grains and high hardness.
2. Tolerance and Straightness
Precision tools demand rods with tight dimensional tolerances and excellent straightness. Check if the supplier can meet standard or custom tolerances like h6, h7, or better.
3. Surface Finish
Some applications require polished or ground rods, especially for applications where tool aesthetics and chip evacuation are important. Ground rods also reduce prep time in your factory.
4. Availability of Customization
As CNC tool manufacturers often design application-specific tools, it's crucial that your carbide supplier can provide:
A. Rods with cooling holes
B. Non-standard lengths
C. Custom diameters
Specific compositions for edge retention or shock resistance
5. Consistent Quality and Batch Stability
A consistent microstructure across batches means fewer tool failures, lower scrap rates, and improved productivity. This is where experienced suppliers like Shanghai Diatooling make a big difference.
The Shanghai Diatooling Advantage
At Shanghai Diatooling, we specialize in providing high-performance solid carbide rods engineered to meet the exacting standards of CNC toolmakers around the world. With our:
A. Superior technological background
B. Advanced R&D capabilities
C. Strict quality control processes
D. High-capacity manufacturing
We can deliver consistent quality in both standard and custom rod sizes. Whether you're producing general-purpose end mills or high-end aerospace reamers, our tungsten carbide experts can help you select the perfect grade and specifications for your tools.
We understand that every CNC tool has a unique purpose, and choosing the right carbide rod is the first and most important step in ensuring tool life and machining performance. Our extensive catalog of grain sizes, cobalt contents, and geometries ensures a tailored solution for every customer.