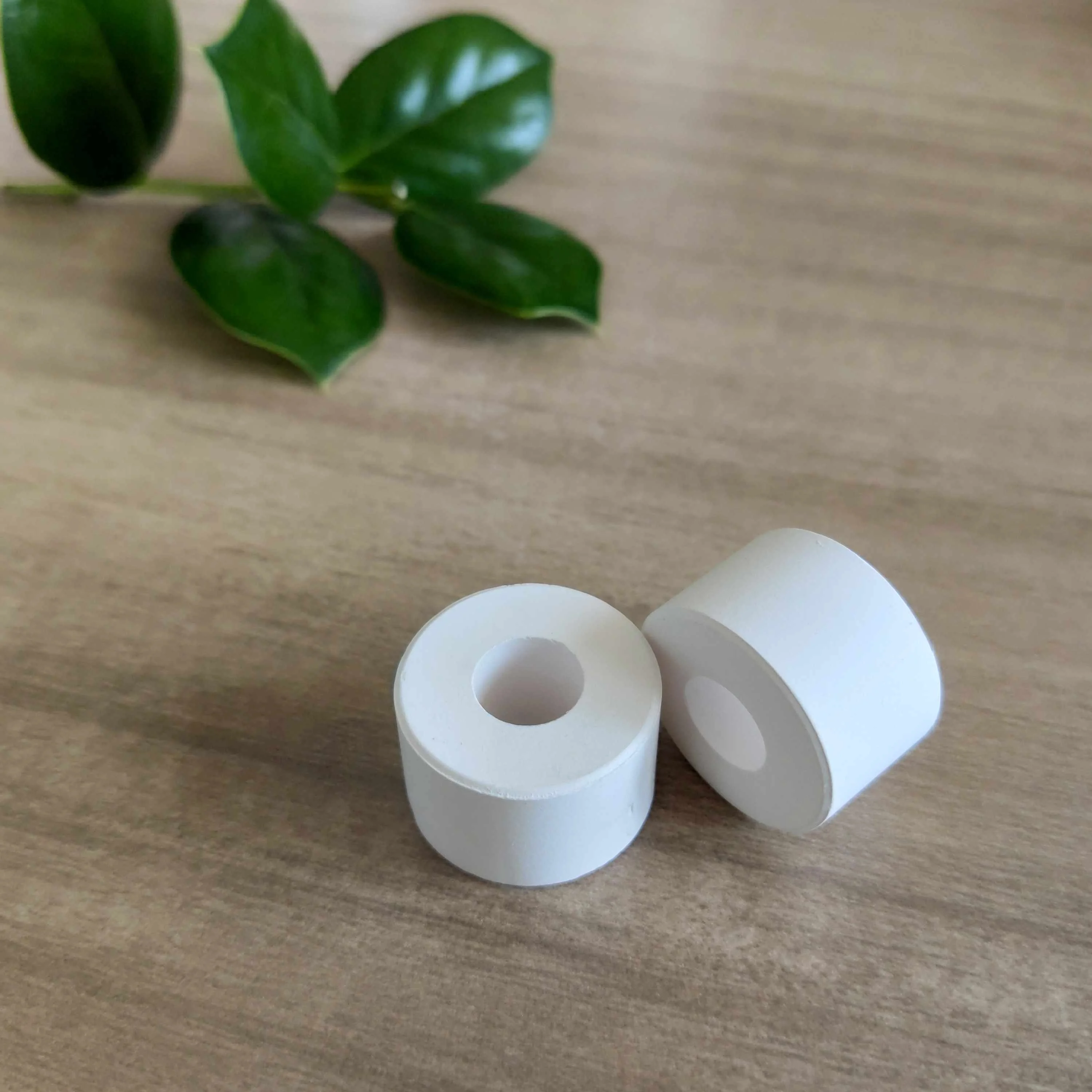
In the world of industrial catalysis, the efficiency and stability of a catalyst system depend not only on the active materials but also heavily on the quality of the catalyst supports. Among various materials available, alumina catalyst supports have become a popular choice due to their excellent physical and chemical properties. However, selecting the right alumina support requires careful consideration of multiple factors to ensure optimal performance in different industrial applications.
In this article, we will explore the key factors you should consider when choosing alumina catalyst supports, and introduce how Yixing Winner Technology Co., Ltd., a leading manufacturer in this field, can support your needs with high-quality solutions.
Understanding Alumina Catalyst Supports
Alumina, or aluminum oxide (Al₂O₃), is prized in catalyst applications for its high surface area, thermal stability, mechanical strength, and resistance to chemical attack. These properties make it an ideal support material across industries such as petrochemicals, environmental protection, and refining processes.
Catalyst supports primarily provide a stable structure that disperses and stabilizes the active catalytic species, preventing sintering and maintaining high activity under operational conditions.
Key Factors to Consider When Choosing Alumina Catalyst Supports
1. Surface Area and Pore Structure
One of the properties of alumina catalyst supports is their surface area. A higher surface area provides more active sites for catalytic reactions, resulting in better performance. Most industrial alumina supports offer a surface area between 100–300 m²/g.
Equally important is the pore size distribution. Depending on the target application (e.g., hydrocracking, reforming, emissions control), you might need different pore sizes:
-
Micropores (<2 nm) for specific small-molecule reactions.
-
Mesopores (2–50 nm) for general catalytic applications.
-
Macropores (>50 nm) for handling large molecules or minimizing pressure drop.
Choosing the correct combination ensures efficient mass transport and reaction rates.
2. Mechanical Strength and Attrition Resistance
In many industrial processes, catalysts are subjected to high mechanical stress during loading, operation, and regeneration cycles. Hence, mechanical strength and attrition resistance are vital characteristics.
Low-quality supports may degrade over time, leading to catalyst fines, blockages, and pressure drops in reactors. Choosing alumina supports with excellent mechanical integrity ensures longer operational life and reduced maintenance costs.
3. Thermal and Chemical Stability
Industrial catalytic reactions often operate under high temperatures and sometimes in corrosive environments. Alumina supports must demonstrate strong thermal stability to withstand sintering and phase transformations at elevated temperatures.
Additionally, chemical resistance against acids, bases, and reaction byproducts is crucial to prevent degradation that could compromise catalyst activity.
4. Purity and Contaminant Levels
Impurities in the catalyst support, such as sodium, sulfur, or chlorine, can poison the active catalyst components, reducing their effectiveness. Therefore, selecting high-purity alumina with minimal trace elements is essential, especially for sensitive catalytic reactions.
5. Shape and Size Customization
The physical form of alumina catalyst supports — such as spheres, extrudates, pellets, or custom shapes — affects reactor packing density, pressure drop, and fluid dynamics.
Choosing the appropriate shape and size ensures efficient use of reactor volume and optimal flow distribution. Some processes require customized dimensions, which reliable manufacturers like Yixing Winner Technology Co., Ltd. can provide based on specific customer requirements.
Why Work with a Professional Manufacturer?
Finding a dependable supplier is just as critical as selecting the right material. Partnering with an experienced manufacturer ensures you receive consistently high-quality products that match your application needs.
Yixing Winner Technology Co., Ltd. is a professional manufacturer specializing in the production of catalysts and their ceramic carriers, ceramic glove formers, and other industrial ceramics. With years of experience and a commitment to innovation, Yixing Winner Technology offers a comprehensive range of alumina catalyst supports that meet stringent industry standards.
The company’s products are known for:
-
High surface areas and tailored pore structures
-
Excellent mechanical and thermal stability
-
Strict control over purity and contaminant levels
-
Flexible customization options for different industries
Their technical support team also provides consultation services to help clients select the most suitable support materials for specific catalytic applications.
Applications of Alumina Catalyst Supports
Alumina catalyst supports are used in a variety of industries, including:
-
Petroleum refining (e.g., hydroprocessing, catalytic reforming)
-
Chemical synthesis (e.g., hydrogen production, ammonia synthesis)
-
Environmental applications (e.g., automotive catalytic converters, industrial flue gas treatment)
-
Renewable energy (e.g., biomass conversion, fuel cells)
Each of these applications demands careful tuning of the support properties, further highlighting the importance of working with knowledgeable suppliers.
Conclusion
Selecting the right alumina catalyst supports involves evaluating surface area, pore structure, mechanical strength, thermal stability, purity, and physical form. By considering these factors carefully, industries can maximize catalyst performance, improve operational efficiency, and extend catalyst life cycles.
If you are looking for reliable and high-quality alumina catalyst supports, Yixing Winner Technology Co., Ltd. stands out as a trusted partner offering premium products and expert solutions tailored to your needs. Their commitment to quality and innovation ensures that your catalytic processes perform at their best, now and into the future.
why alumina catalyst supports are crucial for modern industrial catalysis
www.yxwntec.com
Yixing Winner Technology Co., Ltd.